Copper and energy transition materials
Filling the copper supply gap
Copper is front and center of the energy transition. As a key part of wind turbines, batteries and solar panels, copper demand is set to double in the next 20 years.
We help our customers expand production to meet this demand safely and sustainably. We draw on expertise from our Copper Center of Excellence in Santiago, Chile, supported by our global network of mining and metals specialists, to solve our customers’ challenges.
We specialize in processing plant design, mass materials handling systems, high-capacity concentrators, copper processing, and block cave developments. And we work across both greenfield and brownfield mines. We select the right technology and design to transition to underground mining to access high grade copper ore bodies.
We also help our customers to mine, process and transport other energy transition materials such as lithium, nickel and graphite. These materials are key to electrification, renewable energy, and battery storage technologies.
Statistic Cards
years’ experience delivering copper projects
lithium projects in brine concentrates
years of cross-sector experience
Get in touch
For a greenfield copper-gold mine, this miner wanted to maximize its mineable resources using a multi lift panel cave mining method. However, the deposit has contained heat energy up to 200°C.
Our mining, water resources and oil and gas experts completed a study on pre-mining dewatering from a hot geothermal system using horizontal directional drilling techniques. We found that this could overcome technical risks, bring production forward by 10 months and reduce 61 km of lateral development and five kilometers of vertical development.
It would also reduce costs by US$779 million.
We’re working with CiDRA to complete the front end engineering and design for the full scale implementation of CiDRA’s minerals separation technology at the Carrapeteena mine site.
Applying CiDRA’s technology as a Grind Circuit Rougher will help remove coarse material from the grind circuit circulating loads. Enabling an increase in plant throughput without increasing total power consumption, reducing energy per unit ton by 20 percent.
For a global steel operator, we helped to double their portfolio financial returns per dollar spent, improve risk per dollar spent on safety projects, and increase portfolio transparency and visibility so that improvements were measurable and sustainable.
We created a joint alliance with our customer to achieve these outcomes, which also included an integrated leadership team. This brought rigor and discipline to the portfolio’s processes, including developing business cases and managing gate approvals. It also allowed us to measure financial and risk return as a key performance indicator and drive continuous improvement.
Our project delivery approach
We offer integrated project delivery execution expertise to deliver projects, wherever they are in the world. We're currently providing these services as the Lead Integration Delivery Partner for Rio Tinto's Rincon lithium project in Argentina.
Using technology to create value
We help to reduce the risk of technology adoption by funding pilots, and tracking and testing new innovations.
Copper leaching is a critical component of the copper mining process. And it has a renewed focus in the industry as new leaching technologies and solutions are being developed to ensure a more sustainable copper industry. It consumes less water, removes the need for tailings dams, achieves a metallic copper product, and allows the use of installed capacity.
We have over 50 years of experience in heap leaching, solvent extraction, and electrowinning projects. We’re working closely with our customers and partners to find ways to incorporate new leaching technologies like bioleach, chloride leach, new reagents and catalyst into their copper process so they can unlock high grade resources and increase business value.
A sulphuric acid plant’s safety, efficiency, and reliability plays a critical role in achieving sustainable low cost copper production for both smelting and leaching facilities.
Our Worley Chemetics team helps our customers in the copper industry find solutions to expand the capabilities of their existing acid plants and decrease their environmental impact.
Recognizing the challenges with current ore sorting technologies, Australia’s Commonwealth Scientific and Industrial Research Organization (CSIRO) developed an analyzer for reliable high-throughput ore sensing and sorting, using magnetic resonance technology.
NextOre, our joint venture with RCF Ambrian and CSIRO, brings this technology to market.
NextOre’s magnetic resonance technology can evaluate and sort coarser ore with industry leading accuracy and speed. This brings significant efficiency improvements to miners, allowing them to take a leap forward in sustainability, reduce energy consumption and decrease unit costs.
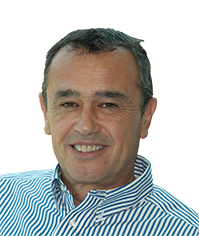