Battery materials:
managing sodium sulphate
managing sodium sulphate
Strategies for a growing byproduct of battery materials production
As global battery production increases, cathode active materials producers have a mounting challenge: sodium sulphate.
How cathode active materials producers manage their sodium sulphate byproduct has a direct impact on their social license to operate, and the viability of their facilities. So, they need to find ways to reduce, reuse, or eliminate it entirely in their processes.
How we help cathode active materials producers
We support our customers in managing their sodium sulphate challenges, helping to avoid project delays and future proof their operations.
We deliver front end studies for our customers working in, or looking to enter, the battery materials sector. And we use our technology partnerships and domain experience to test and apply new technologies to our customers’ flowsheets.
We also design with the end in mind. Our teams provide detailed engineering studies and conduct life-cycle assessments for our customers’ projects. And as concerns around sodium sulphate waste continue to grow, we help develop cathode production pathways that avoid sulphate production all together.
As global demand for battery materials grows, we work with our established technology providers to scale up first of a kind solutions and flowsheets. And we leverage our extensive qualification experience to support material development and facility scale up, in line with end user requirements.
We understand the industry’s challenges with limited bespoke technologies and the growing need for technology advancements to meet customer expectations.
We use our deep technical expertise to diagnose issues, implement solutions and support development to help unlock the potential of our customers’ technologies and products. And ensure they meet end-user qualification requirements.
For producers and projects generating sodium sulphate as part of their existing processes, we offer innovative and sustainable options, supported by robust techno-economic analysis, to tackle their recycling challenges.
Addressing the sodium sulphate challenge for greenfield and brownfield facilities
How can owners reuse, or eliminate, sodium sulphate waste streams from battery materials plants?
The current batteries boom has driven a surge in the volume of sodium sulphate production, at a time when more stringent environmental regulations are making producers dispose of it in more responsible ways.
Engineers as technology partners
Bringing technology to market often involves engaging various partners to support development. How can technology developers achieve this while limiting information disclosure? Our case study provides insights and learnings from current and previous partnerships in technology development, commercialization, and intellectual property strategy and protection.
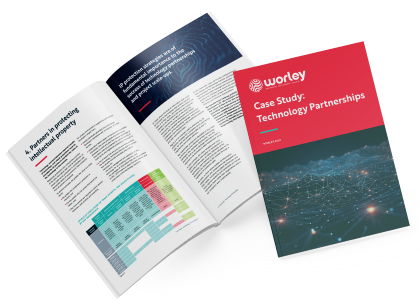
Our work in battery materials
We partner with our customers and other key stakeholders around the world to help build a sustainable supply chain at speed and scale.
We consult, engineer, and construct solutions, from the mining of raw materials through to all the intermediate processing steps for active materials manufacturing and recycling.
Find out more about our global work in battery materials.
Want to find out more?