Daniel Cairns
Senior Technical Consultant
“Throughout my career, I’ve worked in a variety of industries helping to develop more sustainable processes for products or technologies.”
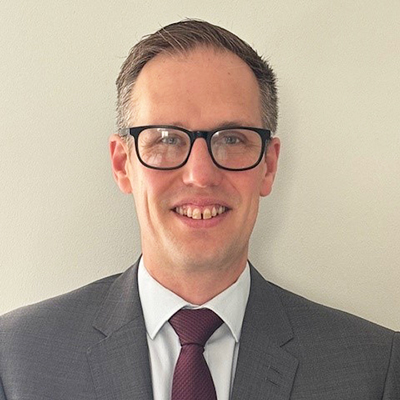
Daniel is part of our Technology and Expert Solutions team, based in Stockton, UK. He uses his technology and innovation experience to deliver front end studies for our customers working in, or looking to enter, the battery materials sector.
“I work with our customers to develop new battery flowsheets and assess alternative technologies, from raw material processing through to battery recycling,” says Daniel.
“The battery materials industry is going through rapid innovation. Working with companies that are generating ideas that can have a long lasting impact on the world is an enjoyable challenge to face each day.”
Technology is advancing but sodium sulphate is a growing concern
The battery material industry has been around for a long time. But for Daniel the exciting part of being in this industry now is that the technology has caught up with customers’ needs.
“This is particularly important when it comes to supporting greenfield battery active material projects,” he says.
“When building on a greenfield site there’s always a concern from investors about the environment impact. And sodium sulphate, the waste by-product of battery active materials (BAM) production, is a growing roadblock for producers and investors.
“A standard lithium-ion cathode active material plant produces more sodium sulphate than it does battery materials,” he explains.
“There are technologies that can convert this waste into higher valuable products for use in a range of different industry sectors. But they require energy, which costs money. It’s a huge challenge. And until the economics are favorable it’s likely there will be stockpiles of sodium sulphate crystals looking for a market.”
New projects must remove sodium sulphate production entirely
Daniel believes it’s critical for new entrants into the industry and new projects, to remove sodium sulphate production from their processes altogether to avoid eventual delays and pushback further down the line.
“Sodium sulphate free processes are key for next generation battery material facilities,” he explains. “And the good thing is these processes already exist and with further developments could become common place.”
“Working on greenfield BAM plants is about starting with a clean slate and being able to design processes that fit the circular economy and will last for decades without harming the environment.”