September 16, 2024 • 3 min read
Fast-tracking critical infrastructure for Germany's gas supply
We worked around the clock to deliver floating LNG terminal in Germany in months, rather than years.
Prior to 2022, Germany sourced over half of its natural gas supply from Russia including from the Nord Stream network that runs beneath the Baltic Sea. But Russia’s invasion of Ukraine in February 2022 triggered an urgent effort to build the infrastructure to import billions of cubic meters of natural gas in a timeframe few thought possible.
The task was twofold. Germany had to find sufficient alternative supplies of natural gas to power millions of homes, schools, businesses, and manufacturing facilities. And it had to establish the infrastructure to access these alternative supplies for the upcoming winter, when demand for heating and power was expected to peak.
A clear goal on a tight schedule
The German government acted quickly, charting five Floating Storage Regasification Units (FSRUs) to build up LNG terminals to access alternative gas supplies.
In June 2022, we were awarded an engineering, procurement, and construction and commissioning contract by the newly founded and federal owned Deutsche Energy Terminal GmbH (DET) to build up one of those terminal projects in Brunsbüttel, Northwest Germany.
“These floating units can receive LNG from cargo ships and feed it into local gas grids,” says Paul Hughes, Project Delivery Vice President. “This means natural gas deliveries can arrive in Germany from anywhere in the world, rather than just by pipeline from the European mainland.
“The goal was to achieve first gas by the following winter of 2022-23. So, the challenge was to design and construct the marine and land infrastructure in a timeframe that would typically take around two years, but in just a few months,” explains Hughes.
“There was no concept or front-end engineering and design (FEED) phase to define what was needed, or exactly how the FSRU would operate. The objective was simply to deliver an LNG terminal to Germany and target first gas during the next winter.”
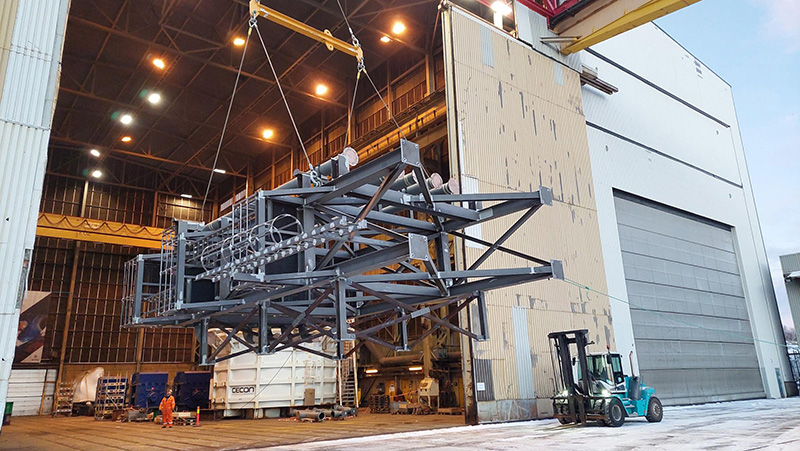
How we accelerated planning and procurement
To tackle the timeline challenge, all parties had to be aligned with the common objective of achieving first gas with a focus on schedule.
“We couldn’t follow a normal project scheduling path,” says Hughes. “We had to look at very different execution sequence from typical large projects, which usually consist of an engineering phase, then procurement, followed by construction in a sequential order. Our plan had to involve out-of-sequence working and reverse engineering based on what critical components we could procure.
“Collaboration and flexibility with the Federal Ministry for Economic Affairs and Climate Action, later with DET was critical. As we were procuring equipment based on preliminary engineering, there had to be acceptance of the risk of change and potential rework depending on what was available in the time we had.”
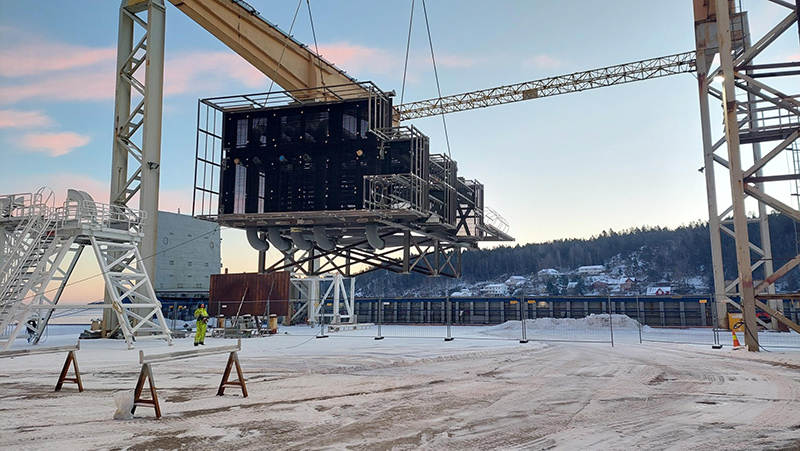
A project team with a global footprint
The fast-tracked execution meant we needed the power of over 200 of our experts from across the world. The project was led from our main UK offices in Aberdeen, Glasgow, Manchester, Stockton and London with engineering and procurement support from Cologne, Stavanger, Baku, Sofia, Madrid, Beijing and our Global Integrated Delivery centers based in India.
“We worked closely with Worley Rosenberg, our fabrication facility in Norway, to simplify the interface between engineering and fabrication, and shorten our timelines,” says Hughes.
“We also took full control of all logistics and freight to avoid any unnecessary delays in equipment and materials. We air freighted the control room from Turkey to Germany instead of shipping it. And we used a helicopter to install the new vent stack onto its foundation. This only took 11 minutes from lifting to bolting down.”
Feeding first gas into the network
We delivered first gas from the LNG terminal into the grid system in less than nine months. We placed the first purchase order in month two, and we started fabrication in month three.
We also met our deadline to have the terminal commissioned, and in operation, in time to deliver natural gas into the grid for the second half of the winter season.
The Brunsbüttel project can now produce up to 3.5 billion cubic metres of gas per year with plans to increase the capacity to 5 billion cubic metres in coming phases.
“We learned a lot from the ambitious task to design, build and commission a floating LNG terminal on such an aggressive schedule,” says Hughes.
“One of the main learnings was how quickly our industry can deliver new infrastructure, by embracing a more agile approach to engineering projects. We don’t always need to follow a sequential process. When we collaborate and embrace new and different ways to deliver complex energy infrastructure, our industry can make the most ambitious projects real.”
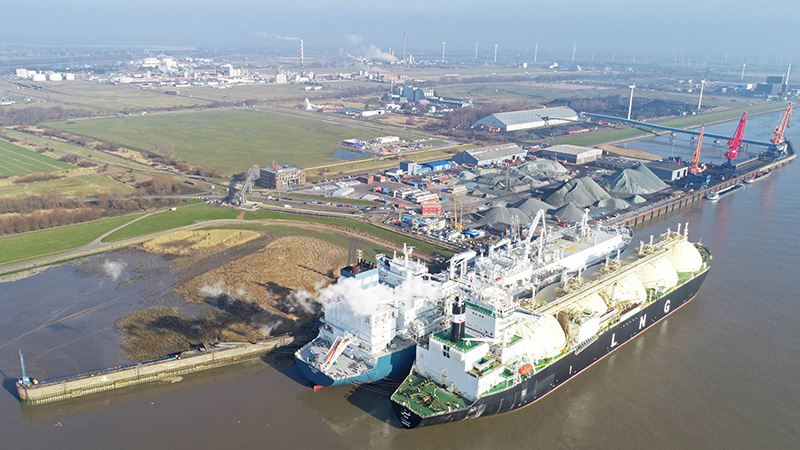
The next phase of the project
We're now supporting Deutsche Energy Terminal GmbH (DET) by undertaking the engineering, procurement, construction and commissioning of the next phase of the project.
"This phase follows a more conventional schedule. Phase 2 involves the new permanent jetty and berth, topsides facilities with new high pressure gas marine loading arms and new water supply to connect with the FSRU."
"Once the infrastructure is completed, the FSRU will be relocated to this new berth to continue operations with the benefit of increased gas flowrates into the grid system."