August 18, 2021 • 2 min read
EPCM for Chevron’s world-first ionic liquid alkylation retrofit
How we helped convert Chevron's existing hydrofluoric acid alkylation unit into a first-of-its-kind facility
Since the 1980s, alkylation capacity has increased steadily due to specifications for higher octane and cleaner-burning gasoline.
Most refinery alkylation units use hydrofluoric or sulphuric acid as the catalyst for the alkylation reaction. However, these are highly corrosive. As a result, operating alkylation plants safely is demanding, and the potential operational inefficiencies are costly.
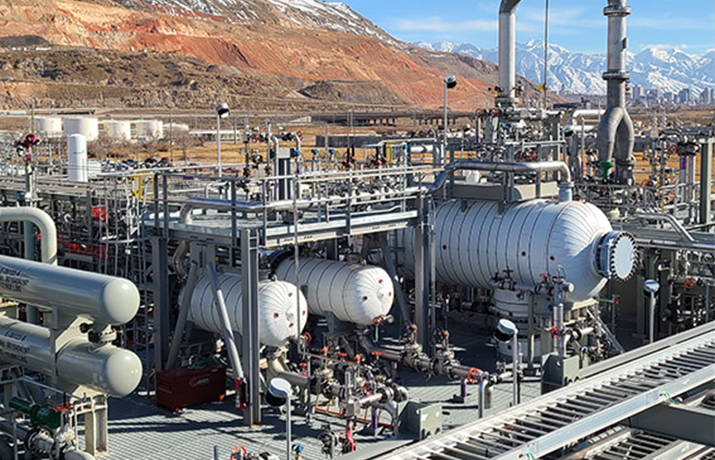
Producing high-octane, cleaner-burning fuels
Chevron developed a new alkylation technology that uses an ionic liquid catalyst to produce high-octane, cleaner-burning fuels. The technology is licensed to the industry through Honeywell UOP, under the ISOALKYTM brand. ISOALKY technology offers comparable costs and performance advantages over existing conventional technologies, which benefit a refinery’s long-term profitability – without the associated acid catalyst issues.
Chevron first tested the new technology at a small pilot plant at its Salt Lake City refinery in Utah, USA, where it operated successfully for five years. As a result, Chevron decided to retrofit its hydrofluoric acid alkylation plant.
“We started conversations with Chevron’s project team and the scientists who worked on the demonstration phase of the project. It soon became apparent that this was a game-changing technology for the industry,” says Haiduk ‘Duke’ Johnas, Worley’s project director. “Being a first-of-its-kind retrofit, it required a ‘one team approach’ with integrated thinking and close collaboration.”
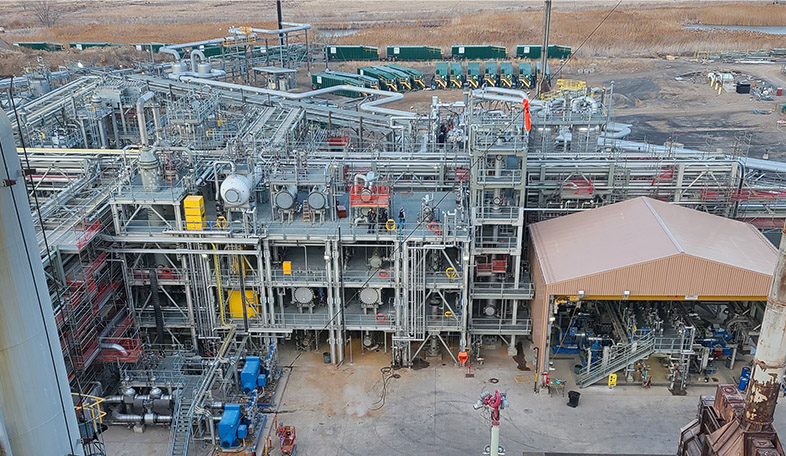
Engineering, fabricating and delivering the world’s first ISOALKY plant
We worked with Chevron to convert the existing hydrofluoric acid alkylation unit into the first-ever ISOALKY alkylation unit. Our scope included pre-FEED, FEED and EPCM and we supported during commissioning and start-up of the unit.
“Hydrofluoric acid alkylation sites require a lot of additional personal protective equipment. As a result, we needed to minimize site construction in and near the existing operating unit, and preferably take it offsite. So, we proposed a customized design using modularization of all the pipe racks, greenfield process areas and equipment skids,” says Johnas.
Through our western Canada fabrication and module assembly business, we fabricated more than 135 modules and skids in Alberta and delivered them to Salt Lake City, Utah. The construction teams reduced rework risk mitigation from the schedule based on the high quality of the work in engineering and modules fabrication, and we shipped all the modules within the required ship dates.
“We installed a huge modular pipe rack and lowered it on top of the existing main rack into supports that we had built. It was a very complex operation, all done safely with no shutdown to operations,” says Johnas.
“Hopefully it’ll be the first of many,” he adds.
Commissioning and start-up of the world’s first ISOALKY process unit was announced in April 2021.

Statistic Cards
ionic liquid alkylation retrofit to the industry in 75 years
fabricated modules
tons of steel, 10,500 cubic yards of concrete and 6,000 welds
weld repair rate in fabrication