December 15, 2020 • 2 min read
Engineering ArcelorMittal Ghent’s industrial bioethanol plant
How we helped turn a circular economy idea into a commercial-scale reality
Carbon dioxide is the primary greenhouse gas emitted on our planet. However, the European Union has set a 2020 target to reduce emissions by 20 percent compared with those in 1990. And for 2050, the objective is to see an 80 to 95 percent cut in emission levels.
In line with these policies, to promote renewable energy and energy efficiency, some companies are already fostering innovation and looking to develop their products in a sustainable way. ArcelorMittal Ghent (AMG) is one of these.
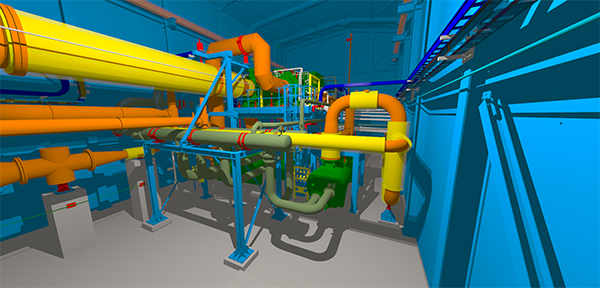
Taking waste gas and producing ethanol
The world’s leading steel company is building a commercial plant at its integrated steel site in Ghent, Belgium, which will convert industrial waste gas from blast furnaces into bioethanol.
Once completed, Steelanol – the first installation of its kind on an industrial scale in Europe – will produce 80 million liters of bioethanol per year. The CO2 reduction is equivalent to greenhouse gas emissions of 250,000 passenger vehicles being driven for one year.
In traditional fermentation, microbes metabolize sugars into chemical compounds, such as alcohols. Lanzatech, a Chicago-based carbon recycling company, has developed a novel technology whereby microbes feed on carbon-rich gas, rather than sugar, and convert them into ethanol. The low-carbon ethanol can be used as a transportation fuel and is a potential building block for plastics and chemicals.
The application of this microbial gas conversion system advances AMG’s carbon capture and enhances steel’s role in the circular economy.
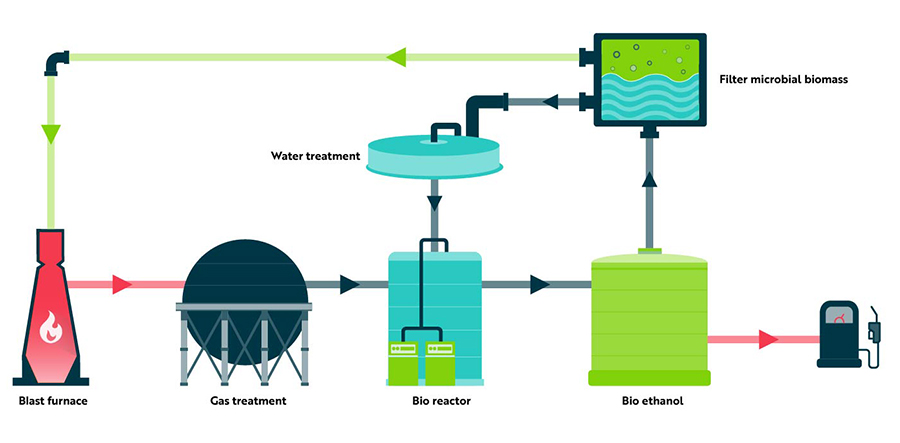
Engineering innovation, from technology to commercialization
We worked closely on the concept, basic and detailed engineering of this project with both AMG and Lanzatech.
As one of Lanzatech’s specialized partners, we translated its technology into an industrial design. During concept engineering, several options were explored to come to an optimum cost versus yield of the installation. During this phase, our process engineers worked with Lanzatech’s technologists on the overall heat and material balance of the plant.
We adopted sustainable water management and optimized the plant’s overall energy integration, recycling over 70 percent of water and minimizing effluent streams and emissions. Another important element during the early project phases was developing the layout. We designed a plant layout that required minimum plot space to reduce the carbon footprint further.
We are currently assisting the customer with preparation of functional specifications, developing AMG’s operations manuals and training their operators.
Training, collaborating, planning and reviewing in virtual reality
We installed a virtual reality set on site for a few weeks, which the customer team used as a walkthrough for a detailed review of the model. This allowed the customer to investigate in detail how certain maintenance activities will need to be done once the plant is up and running. It also meant that the customer’s future operators could obtain a detailed overview of the plant before it was built.
Statistic Cards
of its kind in Europe
liters of sustainable ethanol per year
cars' worth of CO2 emissions saved each year