March 19, 2025 • 4 min read
Optimizing refinery bottom upgrading: smarter technology choices for higher margins and lower emissions
Mike Armstrong, Technical Director from Worley Consulting for Americas Fuels and Chemicals shares his insights on the evolving refining market. With 37 years of experience, he explores the key decisions refiners must make to stay competitive.
The refining industry is at a turning point. With evolving fuel demand, stricter environmental regulations and geopolitical uncertainties, refiners must rethink how they extract maximum value from every barrel.
The challenge is clear: maintain profitability while reducing emissions and adapting to market shifts. The solution lies in selecting the right technology to convert fuel oil and bottom-of-the-barrel residues into high‑value products.
Our global team of consultants help refiners with practical innovative solutions to future proof their assets in an evolving landscape. For example, by looking into technology upgrades from strategy to implementation.
A changing landscape: what’s driving the shift?
There are several factors at play that are reshaping and influencing the industry economics:
- Demand for traditional fuels: Electric vehicle adoption, fleet turnover and changing driving patterns are reducing demand for gasoline, diesel and high carbon fuels like petcoke and fuel oil. Meanwhile, petrochemical demand remains stable, creating an opportunity for refiners to pivot.
- Stronger environmental regulations: Stricter marine fuel regulations and net zero commitments are pushing refiners to cut Scope 1, 2 and 3 emissions, driving investment in carbon capture and cleaner fuels.
- Geopolitical and supply chain challenges: Reliable crude oil availability remains uncertain, making feedstock flexibility and process efficiency more critical than ever.
Refiners must make strategic technology investments that balance operational resilience with environmental responsibility. The question is no longer whether to adapt – but how to do so in the most cost-effective and sustainable way.
Choosing the right technology for refinery upgrades
Selecting the right conversion technology is key to maximizing margins while meeting regulatory and sustainability goals. Through multiple studies, we’ve helped compare technologies providing data driven insights to support informed investment decisions.
We evaluated four options for upgrading fuel oil into petrochemical feedstocks and cleaner fuels.
1. Delayed coking: maximizing conversion, minimizing flexibility
A well-established process, delayed coking thermally cracks heavy residues into lighter products while producing solid petroleum coke. While cost-effective, this method reduces liquid yields and results in high carbon emissions.
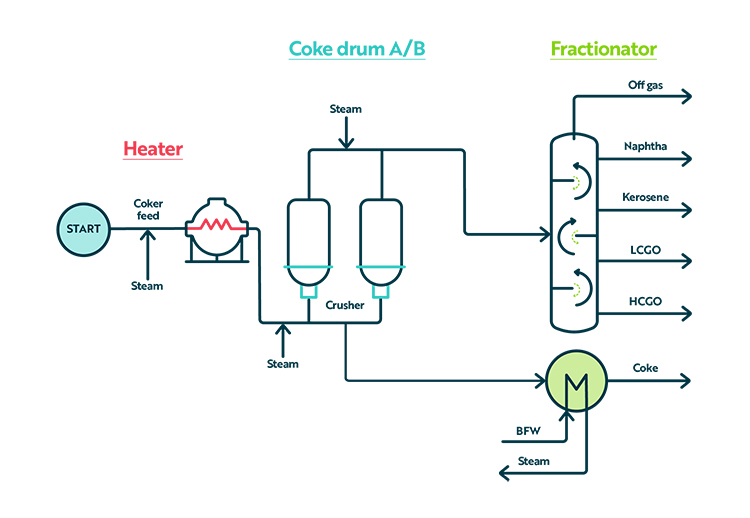
2. Ebullating Bed Hydrocracking (EB Hydrocracking) – a proven, flexible solution
With over 60 years of commercial success, EB Hydrocracking uses a fluidized catalyst to break down heavy residues. This process can produce low sulphur feedstocks suitable for blending, making it an option for refineries looking to meet tighter environmental regulations.
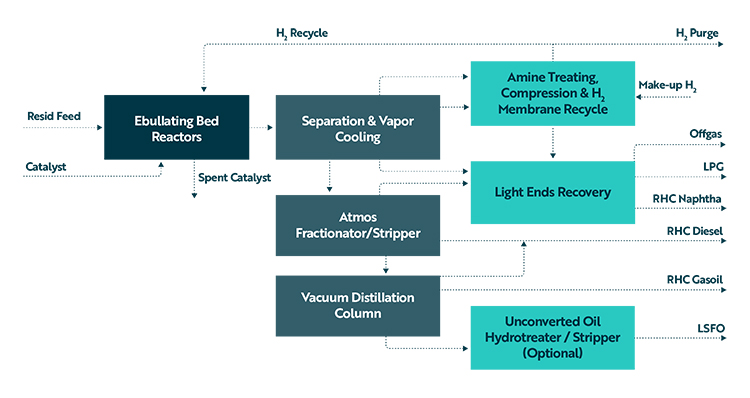
3. Slurry Hydrocracking – high conversion, higher costs
This advanced process uses nanotechnology to suspend tiny catalyst particles in the liquid phase, maximizing conversion. However, it requires high pressure, residence time, and temperature, driving up hydrogen consumption and capital costs. Its unconverted byproducts also hold limited value, making it less competitive.
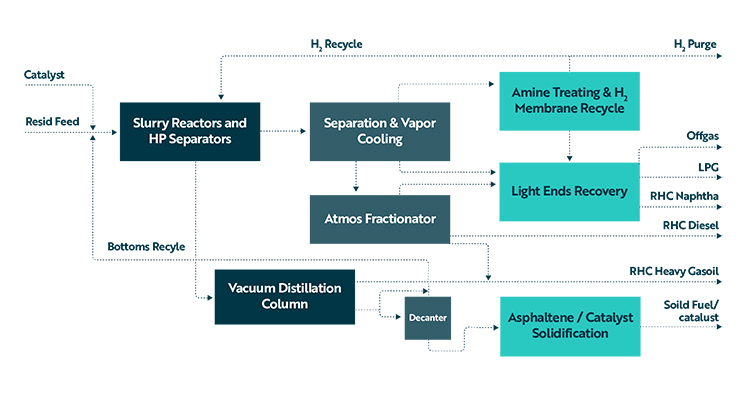
4. Fixed Bed Residue Desulphurization (RDS) – reducing sulphur for cleaner fuels
Primarily used to treat residual fluid catalytic cracking (FCC) and anode grade coke feedstock, RDS reduces sulphur levels in fuel oil, improving its environmental performance. Eliminating downstream hydroprocessing can significantly lower costs for refineries focused on clean fuel production.
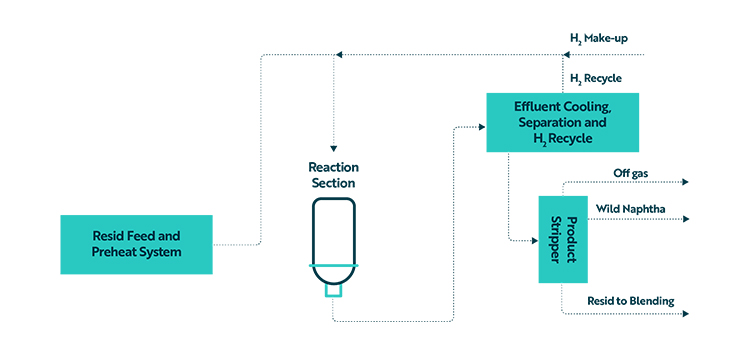
Environmental, technical and financial considerations
Each technology presents trade-offs in emissions, efficiency and economics:
- CO2 emissions: All options require substantial hydrogen, but Slurry Hydrocracking leads in emissions due to higher fuel consumption. EB Hydrocracking requires less hydrogen but more fuel gas and electricity. RDS and Coking have lower hydrogen demands, though Coking still relies heavily on fuel gas firing.
- Product yields: Slurry and EB Hydrocracking significantly increase liquid yields by converting more residue into lighter products. However, Slurry Hydrocracking produces more sulphur and light-end products, increasing hydrogen demand. EB produces a fuel oil product while Coking yields coke and Slurry produces a slurry liquid – both typically sold at lower values compared to oil. RDS on the other hand primarily produces low sulphur fuel oil for marine markets with limited upgrade potential.
- Cost and value retention: Slurry Hydrocracking is the most expensive, while EB Hydrocracking offers a strong balance of conversion efficiency and cost. Coking remains the most cost-effective option but faces sustainability challenges. RDS falls within the mid-range, benefiting from lower downstream hydroprocessing costs.
Other technologies including Vacuum Distillation, Resid Fluid Catalytic Cracking and Solvent De-asphalting can be integrated with these technologies but are less competitive as stand-alone solutions.
Building a strong business case for refinery upgrades
Based on current economics, EB Hydrocracking emerges as the most viable option, offering a balance of conversion efficiency, emissions reduction and product flexibility. Slurry Hydrocracking despite its high conversion rates faces cost and emissions challenges. Coking is less attractive unless fuel oil prices decline due to external factors like shipping decarbonization. RDS remains a strong choice for improving fuel oil quality and margins.
Ultimately, refinery investment decisions depend on location, facility configuration and market conditions. We use techniques such as multi criteria decision analysis to evaluate individual customer and refinery configuration to determine the preferred option for each site.
We actively collaborate with our customers using cash flow models to assess project viability. Our estimates are built using capital cost estimators while yield and energy usage are derived from sophisticated LP modeling. Combined with our industry and technical expertise, we guide refiners through this transition – helping them reduce emissions, improve margins and future-proof their operations in a rapidly evolving industry.
The refining industry is evolving. Are you ready to adapt?